Circuiti stampati HDI PCB FR4 a 6 strati Pcb Gold Fingers
Capacità di processo PCB
NO. | Progetto | Indicatori tecnici |
1 | Strato | 1-60(strato) |
2 | Area di elaborazione massima | 545 x 622 mm |
3 | Spessore minimo della tavola | 4 (strato) 0,40 mm |
6(strato) 0,60 mm | ||
8 (strato) 0,8 mm | ||
10 (strato) 1,0 mm | ||
4 | Larghezza minima della linea | 0,0762 mm |
5 | Spaziatura minima | 0,0762 mm |
6 | Apertura meccanica minima | 0,15 mm |
7 | Spessore rame parete foro | 0,015 mm |
8 | Tolleranza apertura metallizzata | ±0,05 mm |
9 | Tolleranza dell'apertura non metallizzata | ±0,025 mm |
10 | Tolleranza del foro | ±0,05 mm |
11 | Tolleranza dimensionale | ±0,076 mm |
12 | Ponte di saldatura minimo | 0,08 mm |
13 | Resistenza di isolamento | 1E+12Ω(normale) |
14 | Rapporto spessore piastra | 1:10 |
15 | Shock termico | 288 ℃(4 volte in 10 secondi) |
16 | Distorto e piegato | ≤0,7% |
17 | Forza anti-elettricità | >1,3 KV/mm |
18 | Forza anti-strippamento | 1,4 N/mm |
19 | La saldatura resiste alla durezza | ≥6H |
20 | Ritardante di fiamma | 94V-0 |
21 | Controllo dell'impedenza | ±5% |
Realizziamo PCB HDI a 6 strati con 15 anni di esperienza con la nostra professionalità
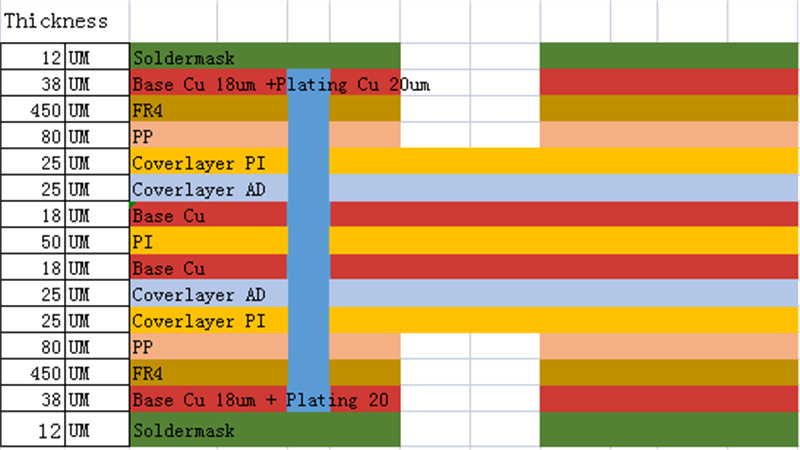
Tavole Flex-Rigide a 4 strati
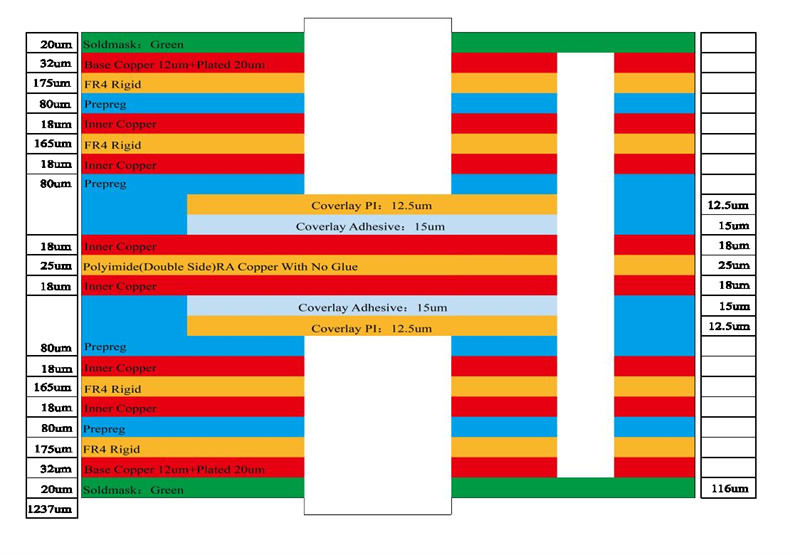
PCB rigidi-flessibili a 8 strati
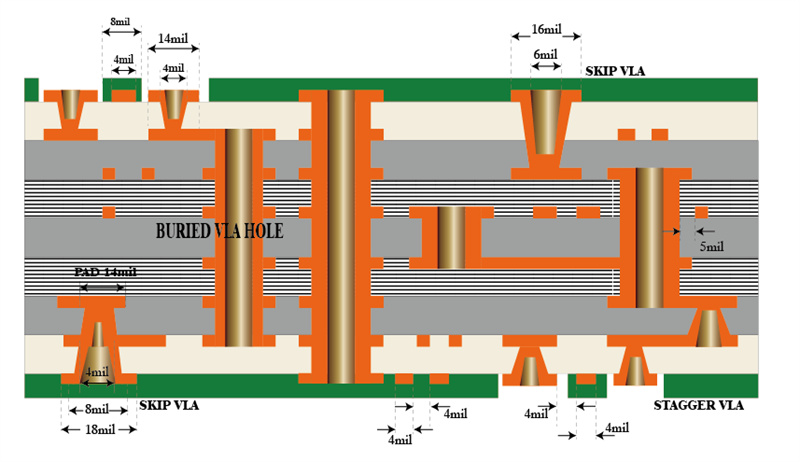
Circuiti stampati HDI a 8 strati
Attrezzature di prova e ispezione
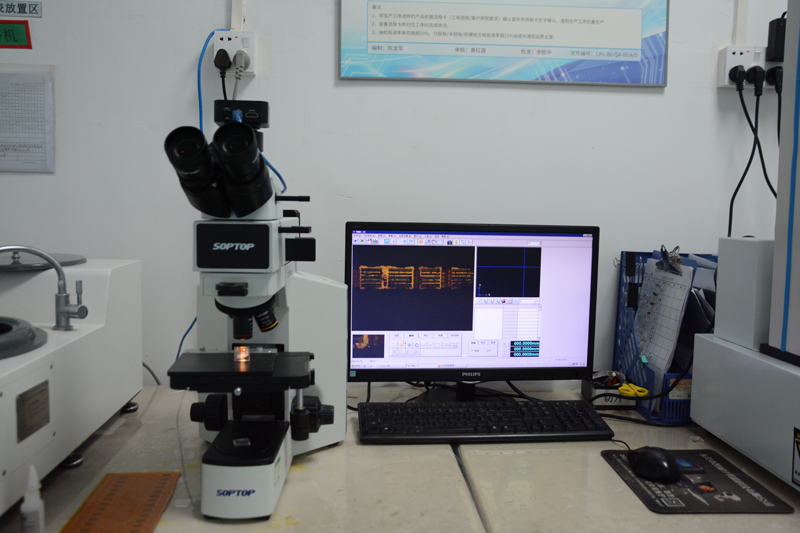
Test al microscopio
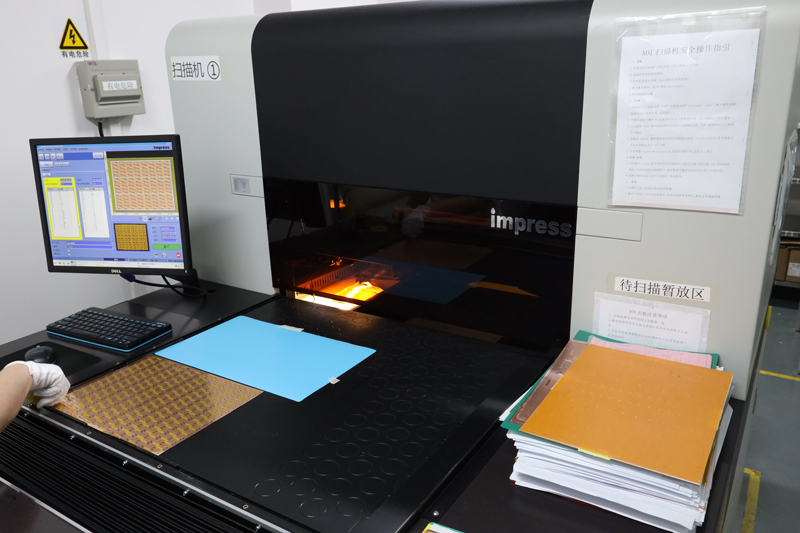
Ispezione dell'AOI
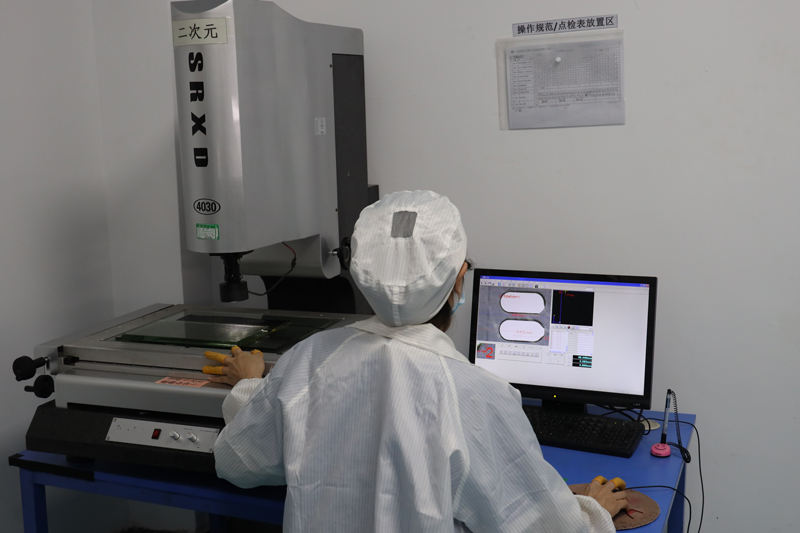
Test 2D
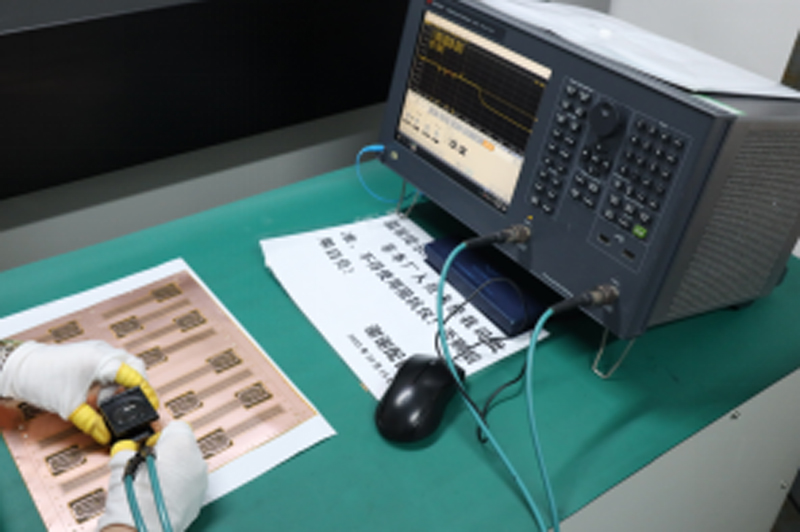
Test di impedenza
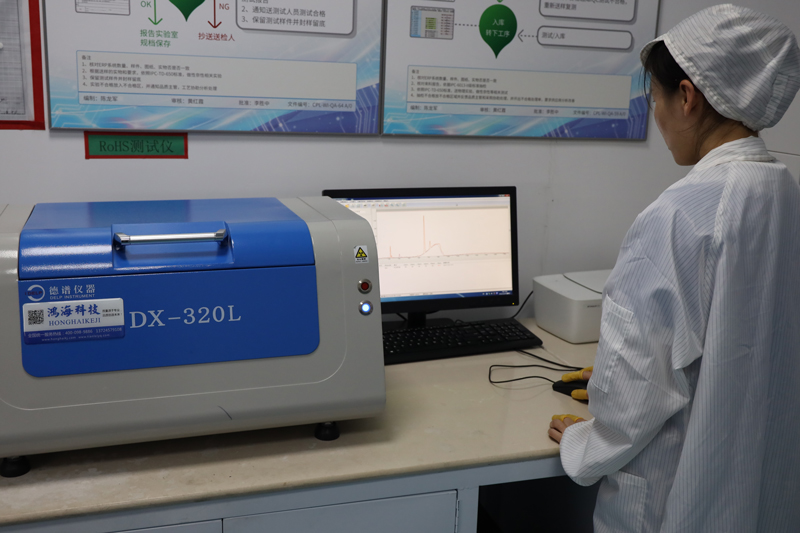
Test RoHS
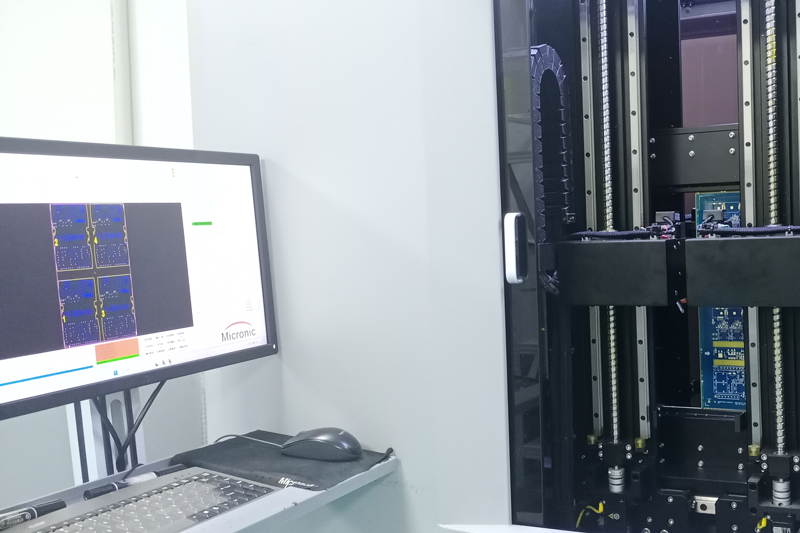
Sonda volante
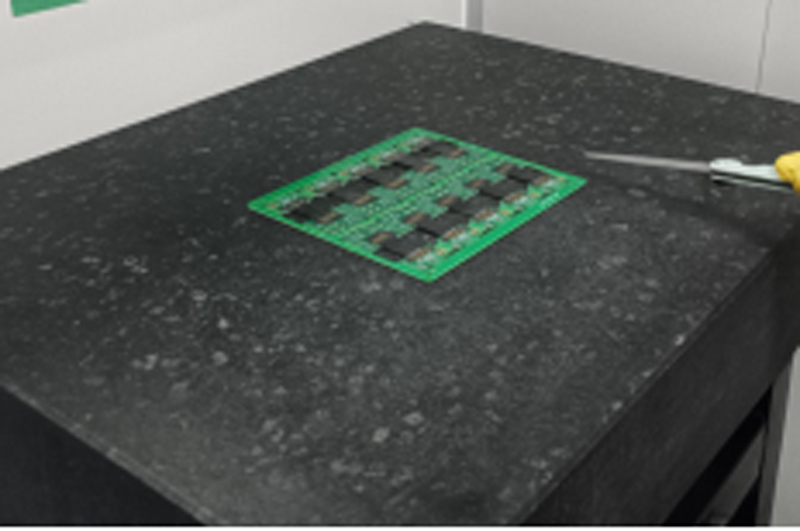
Tester orizzontale
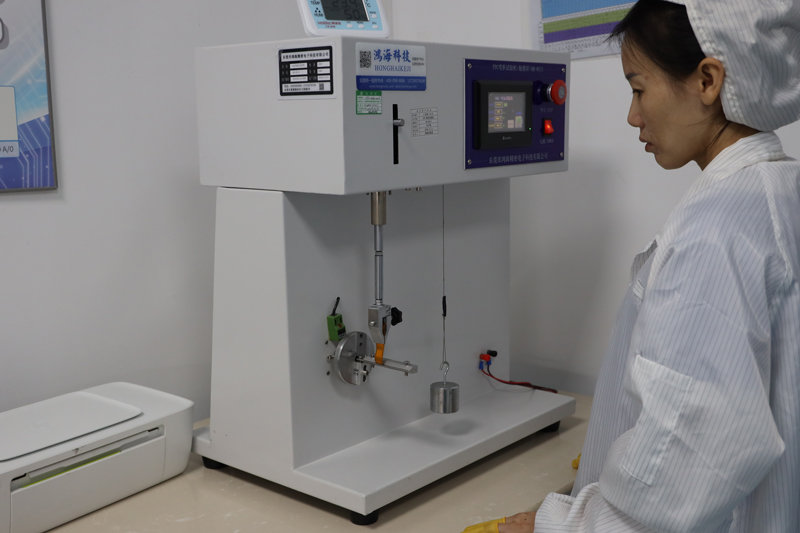
Teste di flessione
Il nostro servizio PCB HDI a 6 strati
. Fornire supporto tecnico pre-vendita e post-vendita;
. Personalizzato fino a 40 strati, 1-2 giorni Prototipazione rapida e affidabile, approvvigionamento di componenti, assemblaggio SMT;
. Si rivolge sia ai dispositivi medici, al controllo industriale, al settore automobilistico, all'aviazione, all'elettronica di consumo, all'IOT, agli UAV, alle comunicazioni, ecc.
. I nostri team di ingegneri e ricercatori si dedicano a soddisfare le vostre esigenze con precisione e professionalità.
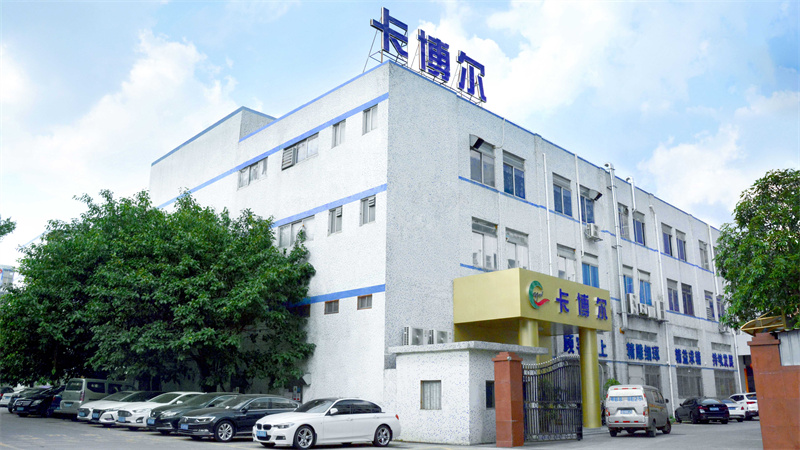
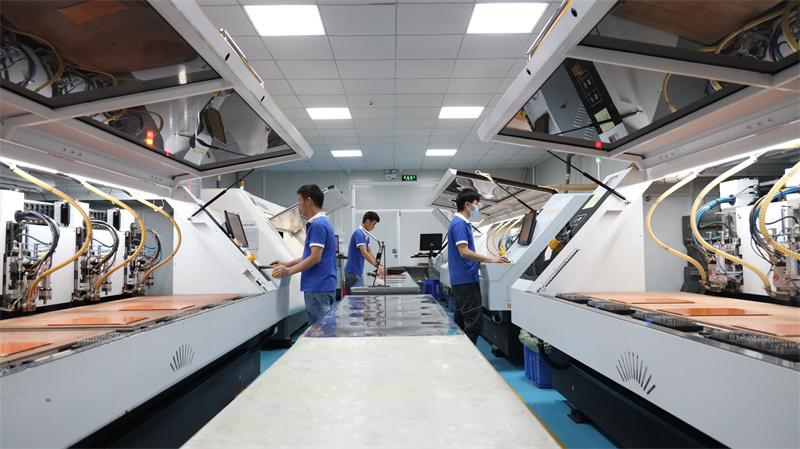
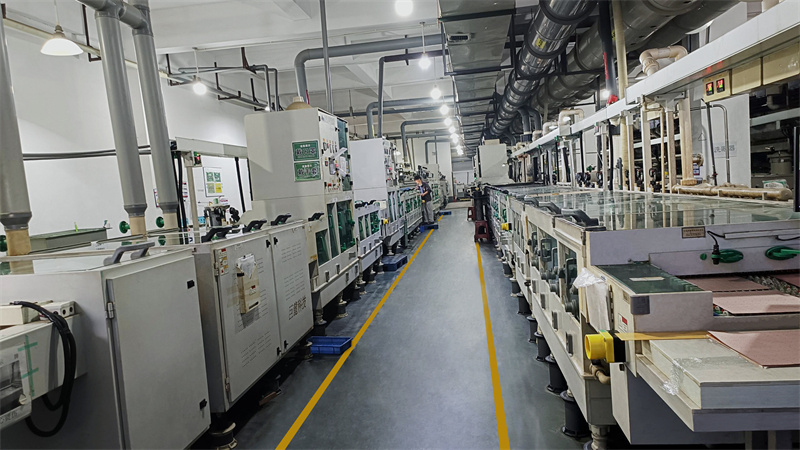
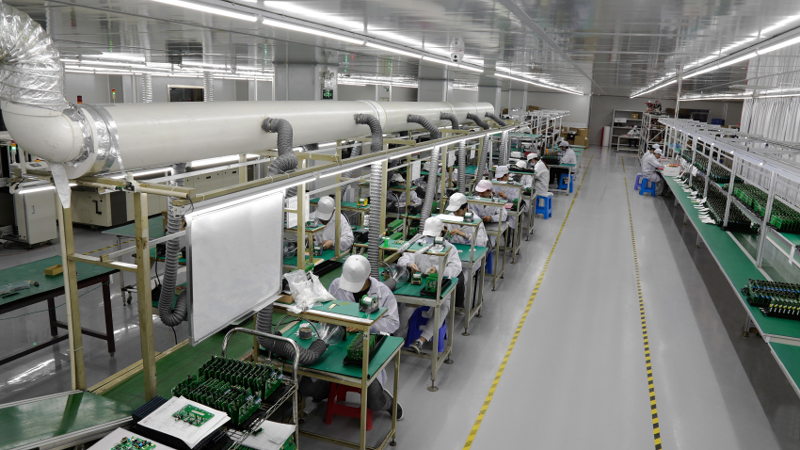
Applicazione specifica PCB HDI a 6 strati nel settore automobilistico
1. ADAS (sistema avanzato di assistenza alla guida): i sistemi ADAS si basano su più sensori come telecamere, radar e lidar per assistere i conducenti nella navigazione ed evitare collisioni. Nei moduli ADAS viene utilizzato un PCB HDI a 6 strati per accogliere connessioni di sensori ad alta densità e garantire una trasmissione affidabile del segnale per un rilevamento accurato degli oggetti e avvisi al conducente.
2. Sistema di infotainment: il sistema di infotainment dei veicoli moderni integra diverse funzioni come la navigazione GPS, la riproduzione multimediale, le opzioni di connettività e le interfacce di comunicazione. Il PCB HDI a 6 strati consente l'integrazione compatta di componenti, connettori e interfacce, garantendo una comunicazione efficiente, un controllo affidabile e un'esperienza utente migliorata.
3. Unità di controllo del motore (ECU): l'unità di controllo del motore è responsabile del monitoraggio e del controllo di varie funzioni del motore come l'iniezione del carburante, la fasatura dell'accensione e il controllo delle emissioni. Il PCB HDI a 6 strati aiuta a ospitare circuiti complessi e comunicazioni ad alta velocità tra diversi sensori e attuatori del motore, garantendo controllo preciso ed efficienza del motore.
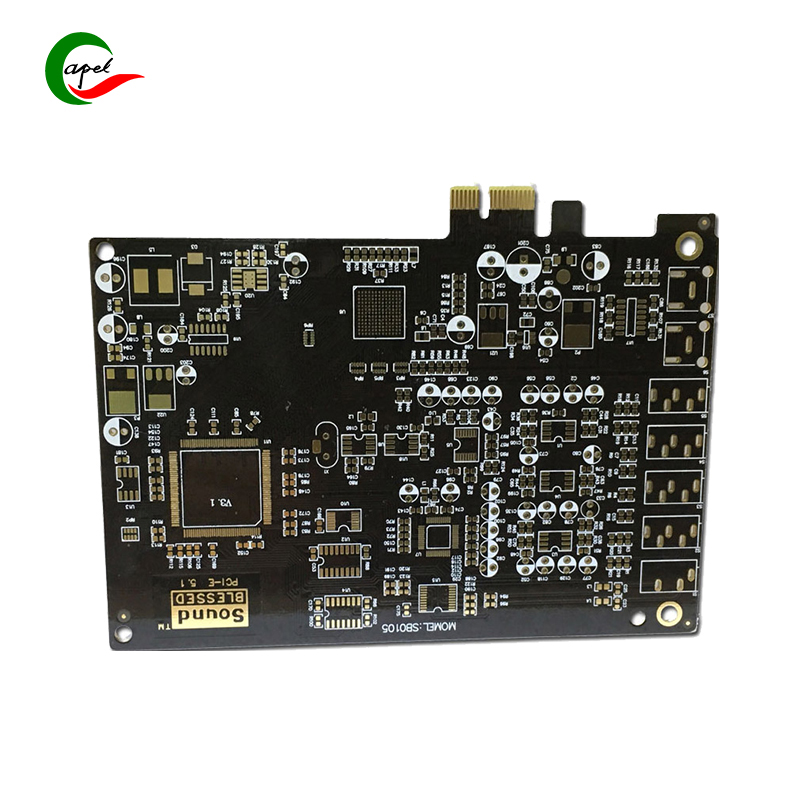
4. Controllo elettronico della stabilità (ESC): il sistema ESC migliora la stabilità e la sicurezza del veicolo monitorando e regolando continuamente la frenata delle singole ruote e la coppia del motore. Il PCB HDI a 6 strati svolge un ruolo fondamentale nel modulo ESC, facilitando l'integrazione di microcontrollori, sensori e attuatori per l'analisi dei dati in tempo reale e un controllo preciso.
5. Gruppo propulsore: l'unità di controllo gruppo propulsore (PCU) regola il funzionamento del motore, della trasmissione e della trasmissione per prestazioni ed efficienza ottimali. Il PCB HDI a 6 strati integra vari componenti di gestione dell'alimentazione, sensori di temperatura e interfacce di comunicazione, garantendo un trasferimento di potenza efficiente, uno scambio di dati affidabile e un'efficace gestione termica.
6. Sistema di gestione della batteria (BMS): il BMS è responsabile del monitoraggio e del controllo delle prestazioni, della ricarica e della protezione della batteria del veicolo. Il PCB HDI a 6 strati consente la progettazione compatta e l'integrazione di componenti BMS, inclusi circuiti integrati di monitoraggio della batteria, sensori di temperatura, sensori di corrente e interfacce di comunicazione, garantendo una gestione accurata della batteria e prolungandone la durata.
In che modo il PCB HDI a 6 strati migliora la tecnologia nel settore automobilistico?
1. Miniaturizzazione: il PCB HDI a 6 strati consente il posizionamento di componenti ad alta densità, realizzando così la miniaturizzazione dei sistemi elettronici. Questo è fondamentale nel settore automobilistico dove lo spazio è spesso limitato. Riducendo le dimensioni del PCB, i produttori possono progettare veicoli più piccoli, leggeri e compatti.
2. Migliora l'integrità del segnale: la tecnologia HDI riduce la lunghezza delle tracce del segnale e fornisce un migliore controllo dell'impedenza.
Ciò migliora la qualità del segnale, riduce il rumore e migliora l'integrità del segnale. Garantire prestazioni affidabili del segnale è fondamentale nelle applicazioni automobilistiche in cui la trasmissione e la comunicazione dei dati sono fondamentali.
3. Funzionalità migliorata: i livelli aggiuntivi in un PCB HDI a 6 strati forniscono più spazio di instradamento e opzioni di interconnessione, consentendo funzionalità migliorate. Le auto ora integrano una varietà di funzioni elettroniche, come sistemi avanzati di assistenza alla guida (ADAS), sistemi di infotainment e unità di controllo del motore. L'uso del PCB HDI a 6 strati facilita l'integrazione di queste funzioni complesse.
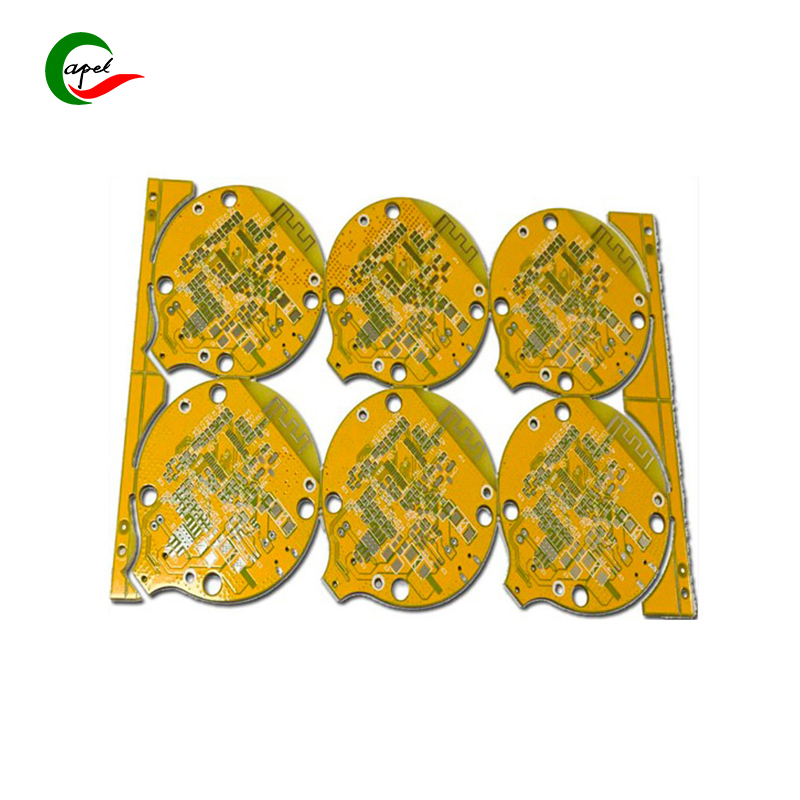
4. Trasmissione dati ad alta velocità: i sistemi automobilistici, come i sistemi di navigazione avanzati e la comunicazione tra veicoli, richiedono una trasmissione dati ad alta velocità. Il PCB HDI a 6 strati supporta applicazioni ad alta frequenza per una trasmissione dei dati più rapida ed efficiente. Questo è fondamentale per il processo decisionale in tempo reale, migliorando la sicurezza e le prestazioni.
5. Maggiore affidabilità: la tecnologia HDI utilizza micro-vie per fornire migliori connessioni elettriche occupando meno spazio.
Questi via più piccoli aiutano a migliorare l'affidabilità riducendo il rischio di diafonia del segnale e disadattamento di impedenza. Nell'elettronica automobilistica, dove l'affidabilità è fondamentale, i PCB HDI garantiscono connessioni robuste e durevoli.
6. Gestione termica: con la crescente complessità e consumo energetico dell'elettronica automobilistica, una gestione termica efficiente è fondamentale. Il PCB HDI a 6 strati supporta l'implementazione di vie termiche per aiutare a dissipare il calore e regolare la temperatura.
Ciò consente ai sistemi automobilistici di funzionare in modo ottimale, anche a temperature elevate.